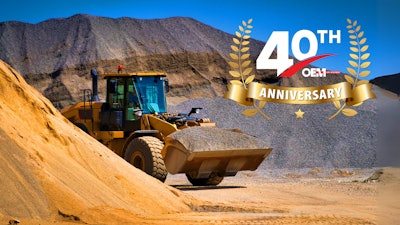
As OEM Off-Highway marks its 40th anniversary in 2024, we reflect on the incredible journey the brand — and the industry as a whole — has had over the past four decades. From humble beginnings to becoming a staple of the industry, OEM Off-Highway has been a platform for showcasing innovation, excellence and progress.
To mark this significant milestone, we're exploring both the past and the future. In our continued coverage, we take a look at some of the more sizeable shifts and track the trends that have helped to shape off-highway equipment as we know it today.
The off-road machinery manufacturing sector continually evolves as manufacturers chase the next competitive edge that elevates customer expectations. The pace of that change kicked into high gear as the industry moved into an era where computers, data and the emergence of sophisticated electronics transformed the off-highway manufacturing landscape. With each passing year the pace of change picks up momentum, making it more challenging for OEMs to stay abreast of these developments.
Recognizing a growing demand for information, OEM Off-Highway magazine positioned itself as an information source in this dynamic landscape. Its initial emphasis in the early 1990s was centered on rapidly changing manufacturing processes as OEMs sought to enhance efficiency.
Streamlining the Manufacturing Process
The early 1990s marked a period of significant transformation in the supply chain and the production methods employed on the factory floor. The Toyota production method gained traction among North American OEMs during this time. At its core, this production method eliminates waste by making only what is needed by the customer precisely when needed and in the necessary quantity.
Manufacturers sought out best practices and insights that would help them adopt many of the Toyota production principles. OEM Off-Highway was there to provide a source of this information.
I joined the OEM Off-Highway staff in 1992 and was excited to put my Engineering Operations degree to use. I was fortunate to travel across North America, touring manufacturing facilities as they transformed their manufacturing processes.
OEMs and their suppliers happily shared how they implemented Kanban carts with parts kitted to increase production efficiency and just-in-time inventory practices that opened up valuable manufacturing real estate. The supply chain was in the midst of a transformation with parts delivered to the production line precisely when needed. The traditional practice of warehousing components on site and the associated carrying cost was quickly becoming history.
Amid this backdrop, Henry Ford’s mass production line process was being revolutionized to transform workers into teams that could drive efficiency improvements. The industry began moving away from industrial engineers performing time studies and recommending process improvements to empower the people performing the work to make these improvements. This resulted in rapid productivity increases that many OEMs were willing to share.
In many cases, manufacturing teams were organized by cells that performed a certain critical task in the manufacturing process. These teams were then empowered to discover and implement efficiency and quality improvements. In many cases, OEMs would proudly explain that when any employees spotted defects in the product traveling down the manufacturing line, they had the authority to stop the line so the problem could be corrected.
It was fascinating to observe how each manufacturing plant had a unique personality and how two companies producing a similar product could take vastly different approaches to production. As manufacturing teams contributed ideas to enhance efficiency, we saw remarkable innovations in how each company tackled production and assembly processes.
Automation Drives Quality & Efficiency
In the 1990s factory automation gained momentum, with robotic welding becoming a widespread practice to guarantee consistent quality. Unlike humans, who might need to reposition the workpiece resulting in variations between welds, the robotic welder could seamlessly weld the same components all day long with perfect consistency.
Many tasks previously completed by hand were now performed to exact tolerances by machines. One engine manufacturer we visited automated a large portion of the engine block assembly process. Machines applied an ideal amount of sealant in the exact location to form the perfect gasket every time. All head bolts were torqued to the exact specifications. Production employees then finished the final assembly.
Enhanced tools and automation not only enhanced productivity but also alleviated physical strain on workers. Bolts were automatically torqued to spec with the torque values being captured and recorded. In many cases, assembly line workers no longer had to contort themselves into unnatural positions to complete tasks. Furthermore, heavy components like engine blocks could be efficiently rotated or positioned for optimal access at the next assembly station.
Production Workers See Major Environmental Improvements
During a few short years, we witnessed many manufacturing lines undergo a dramatic transformation as natural light and outside air were piped into the production line workers and ergonomics became a major focus. This included everything from the flooring workers stood on to the production tools used to assemble the products. These changes were not only beneficial for employee retention but also resulted in increased productivity.
As the production line transformation progressed, there was a renewed focus on defining manufacturing processes. ISO 9001:2000 quality management emerged as a way manufacturers could demonstrate their ability to produce consistent product quality. Many manufacturers began to pursue certification to this international standard. Processes were painstakingly documented to ensure repeatable results.
Emission Regulations Change the Landscape
The emergence of diesel emissions standards in the 1990s changed the product development cycle for diesel-powered equipment, which continues to reverberate through the industry until this day. The first Tier 1 diesel emission standard was published in 1991 and took effect in 1996. It set limits on NOx emissions on engines over 50 hp.
This was followed by a series of increasingly stringent regulations in the form of Tier 2, Tier 3, Tier 4 interim and Tier 4 final. Each stage included tighter emissions limits for NOx and Particulate Matter (PM) broken out by engine horsepower.
This was not merely a challenge faced by the engine suppliers. Increased heat rejection and changing engine footprints required OEMs to constantly invest R&D dollars to modify the machines at each Tier. Additional space was needed as diesel particulate filters, oxidation catalysts and diesel exhaust fluid (DEF) tanks found their way onto construction equipment.
At each Tier of emissions, the OEM R&D departments were challenged to maintain fuel efficiency and increase performance to help offset the mandatory increase in complexity and cost. For instance, mechanical engines transitioned to electronically controlled engines. This opened a whole realm of new possibilities for many OEMs.
With advanced electronic controls (ECUs) now on the machines, engineers could tie components into ‘smart’ systems where the engine, transmission and other critical components could communicate with each other. New productivity-enhancing features began to emerge.
GPS Transforms Earthmoving & Tracking
In the late 1990s into the early 2000s GPS technology promised to transform the earthmoving industry. Early indicate only earthmoving systems followed by more automated technology promised to replace the manual and labor-intensive process of pounding in grade stakes on earthmoving sites.
This technology was also changing the way manufacturers viewed earthmoving machines. GPS grade control was in its infancy, but the R&D departments were already looking at ways to integrate this technology into the machines. However, it took several more years before GPS grade control systems became widely adopted. Now grade control technology is virtually a necessity for large earthmoving projects and many of the large OEMs offer machine-integrated grade control.
GPS technology also proved useful for machine location and as the technology was integrated into emerging telematic systems, manufacturers stepped into the fleet management business.
Looking Toward the Future
When contemplating how the industry has changed since the 1990s, it’s hard to imagine how current realities will drive further change in OEM operations. The COVID-19 pandemic highlighted vulnerabilities in the supply chain which made some manufacturers pad Just in Time inventories with a little more Just In Case.
However, most of the efficiencies gained from the transformation of the manufacturing process continue to drive OEM success. While there are still efficiencies to be gained, the conversation has turned to new growth opportunities including the Internet of Things, Big Data and autonomy. Staying on top of the latest needs, the media serving this audience has also evolved.
Some key challenges from the 1990s still exist, such as the severe shortage of skilled labor and the challenge to provide value to customers in the face of ever more stringent emission regulations. Yet, a new set of challenges constantly emerge, and the pace of change continues to accelerate. Looking back, the 1990s was an exciting time for off-highway OEMs, but the challenges pale in comparison to the changes on the horizon.
For more on OEM Off-Highway's 40th anniversary, check out our additional and extended coverage.