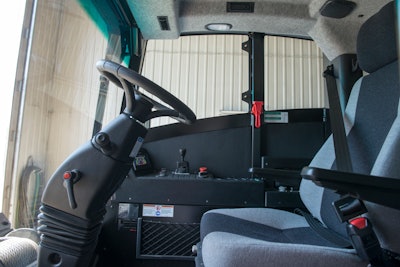
Crawler carriers play a crucial role in the ever-evolving world of off-highway equipment, from construction, to oil and gas, to utilities and far beyond. As these sectors face increasing pressure to improve efficiency, reduce environmental impact and enhance operator comfort, the crawler carrier market is experiencing a significant transformation. This article examines the current state of crawler carrier technology and explores areas where the industry can focus its efforts to meet the growing demands of the market.
How climate control goes beyond basic comfort
Climate control in crawler carriers has long been viewed as a luxury rather than a necessity. However, as we push the boundaries of where these machines can operate, from scorching deserts to frigid arctic environments, advanced climate control systems are becoming essential for operator comfort and machine performance.
Industry leaders are now incorporating sophisticated HVAC systems as standard features, moving away from the days when air conditioning was an optional extra. These systems not only ensure operator comfort in extreme temperatures, but also contribute to increased productivity and extended work hours. For instance, in southern regions of the United States, where temperatures can soar, a well-designed climate control system can make the difference between a full day’s work and frequent breaks due to heat exhaustion.
Moreover, some manufacturers with broad equipment offerings are leveraging unique technologies developed for cold climate applications to enhance their crawler carriers’ climate control capabilities. Features such as windscreen de-icing systems, which combine forced air circulation glass heated by embedded filaments, ensure clear visibility in cold and humid conditions. This technology, originally designed for vehicles operating in harsh winter environments, is now finding its way into crawler carriers, expanding their operational range and reliability in diverse climates.
Figure 1: Crawler carriers are versatile enough for applications in off-highway construction, mining, utility infrastructure, oil and gas, environmental reclamation and more.Prinoth Ltd.
Comfort and ergonomics is key to operator retention
As the skilled labor shortage continues to challenge the construction and off-highway industries, operator comfort and ergonomics have become critical factors in equipment design. The most advanced crawler carriers now boast cab designs that rival the comfort of high-end automobiles by featuring spacious interiors, ergonomic controls and superior visibility.
One significant trend is the adoption of automotive-style controls, such as steering wheels and foot pedals, replacing the traditional levers found in many older models. This approach not only reduces operator fatigue during long shifts, but also shortens the learning curve for new operators, addressing the industry’s need for quicker training and onboarding.
Adjustable, air-suspended seats with lumbar support and ergonomically-designed armrests are becoming the norm. Some manufacturers are even introducing electric seats, allowing operators to find the optimal position for different tasks and improving visibility in all directions.
Some modern crawler carriers are also equipped with cabs that meet rigorous roll-over protective structure (ROPS) and falling object protective structure (FOPS) standards, providing crucial protection for operators. These certifications underscore the industry's commitment to operator safety, ensuring the cab can withstand significant impact and still maintain its structural integrity in hazardous situations.
The emphasis on operator comfort, safety and wellbeing extends beyond the physical aspects of the cab. Noise reduction technologies, including improved insulation and engine placement, are creating quieter work environments, reducing operator stress and fatigue over long work hours.
Figure 2: As the industry grapples with skilled labor shortages, advanced crawler carriers are prioritizing operator comfort and ergonomics with automotive-style cabs and controls, enhancing retention and easing training.Prinoth Ltd.
Simplifying complex tasks
The complexity of operating heavy equipment has long been a barrier to entry for new operators. However, the latest crawler carriers are incorporating technologies that simplify operation without compromising capability.
One notable innovation is the introduction of automated systems for tasks that used to require significant operator skill. For example, some models now feature automatic track tensioning systems, which reduce maintenance requirements and ensure optimal performance without constant operator attention.
Inclinometers with visual and soon audible alarms are becoming standard, providing real-time feedback on machine stability and helping operators navigate challenging terrain safely. Some advanced models are even incorporating adaptive control systems that learn the characteristics of various attachments and optimize performance, reducing the need for manual adjustments.
Another area of focus is the interface between operator and machine. Touch-screen displays with intuitive, customizable interfaces, providing operators with clear, relevant information, are replacing traditional gauge clusters. These systems often include on-board diagnostics, which simplify troubleshooting and reduce downtime.
Enhancing safety and productivity
In the crawler carrier market, visibility is not just about operator comfort—it’s a critical safety feature that impacts productivity. Leading manufacturers are redesigning cab structures to maximize visibility, with some models offering nearly 360-degree views of the surrounding area.
Large, panoramic windshields and floor-to-ceiling side windows are becoming more common, as are sloped hood designs that improve forward visibility. These design changes not only enhance safety by reducing blind spots but also increase efficiency in tasks that require precise positioning, such as working near excavations or in tight spaces.
Supplementing direct line-of-sight visibility, camera systems are now standard on many models. Rear-view cameras are very common with some manufacturers offering multi-camera systems that provide a bird’s-eye view of the entire machine and its surroundings. These systems are valuable in congested worksites or when maneuvering in confined spaces.
Figure 3: Manufacturers are adapting advanced cold-climate technologies, such as windscreen de-icing systems, to enhance crawler carriers' climate control and visibility, extending their operational range in diverse environments.Prinoth Ltd.
Fleet management’s future in connectivity, telematics
Perhaps the most transformative trend in crawler carrier technology is the integration of advanced connectivity and telematics systems. These technologies are revolutionizing how equipment is managed, maintained and operated.
Some manufacturers offer telematics dashboards that enable fleet managers to monitor all vehicle operational data remotely. This includes real-time information on fluid levels, engine temperature, operating hours and much more.
These systems also allow fleet managers to virtually view all instrumentation the driver sees in the cab, providing unprecedented insight into machine operation and performance. This level of remote monitoring not only enhances operational efficiency but also aids in predictive maintenance, reducing downtime and extending equipment life.
Modern telematics systems also provide real-time data on machine location, operating hours, fuel consumption and performance metrics. This information allows fleet managers to optimize equipment utilization, schedule preventive maintenance more effectively and identify opportunities for operator training.
Data gathered from these systems also may help manufacturers design better products in the future. The engineering of newer generations of equipment will be predicated upon deep insight into operator and fleet managers behaviors, as well as equipment performance under different circumstances.
Some manufacturers are taking this a step further by offering remote diagnostics capabilities. These systems can alert maintenance teams to potential issues before they lead to breakdowns, reducing downtime and repair costs. Some manufacturers even have the capability of delivering wireless software updates that can be deployed remotely, ensuring equipment always operates with the latest improvements and bug fixes.
The integration of telematics data with broader fleet management software is creating new opportunities for efficiency. For example, some systems can now provide automated maintenance scheduling based on actual usage rather than calendar time, ensuring equipment receives service without unnecessary downtime.
Meeting stricter emissions standards
As environmental regulations become more stringent worldwide, crawler carrier manufacturers are focusing on employing cleaner, more efficient power systems. The latest models often feature engines that meet or exceed the most stringent emissions standards, such as Tier 4 Final in the United States and Stage V in Europe.
Beyond meeting regulatory requirements, some manufacturers are exploring alternative fuel options, including biodiesel compatibility and even hybrid or fully electric power systems for certain applications. While these technologies are still in their early stages for crawler carriers, they represent a significant area of future development as the industry seeks to reduce its environmental footprint.
A holistic approach to crawler carrier advancement
The crawler carrier market is at a pivotal point in its evolution. The convergence of advanced technologies, changing workforce dynamics and increasing environmental concerns is driving rapid innovation across all aspects of machine design and operation.
It’s clear the most successful crawler carrier companies will be those that take a holistic approach to advancement. This means not only incorporating the latest technologies, but also ensuring these innovations work together to enhance overall performance, efficiency and operator experience. For those manufacturers with broad market experience, cross pollinating technologies will continue to enhance vehicle design.
For fleet managers and equipment purchasers, this evolution presents opportunities and challenges. While the latest crawler carriers offer unprecedented levels of productivity and efficiency, they also require a more sophisticated approach to operation and maintenance. Investing in operator training and embracing new fleet management technologies will be crucial to realizing the full potential of these advanced machines.
As the industry continues evolving, close collaboration between manufacturers, operators and end-users will be essential. By focusing on real-world needs and applications, the crawler carrier market can ensure technological advancements translate into tangible benefits on the job site, driving progress across the off-highway construction, oil, gas and utility sectors.