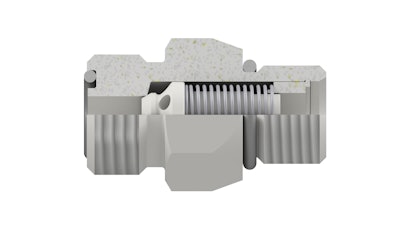
A standard check valve’s function is to only allow flow in one direction. However, there is still quite a bit of variety in the types of check valves on the market. There are two primary choices when specifying the sealing method of a check valve — hard or soft. While both function similarly, they differ in the way that they seal when they are not allowing flow.
With a hard seat valve, there is metal-on-metal contact forming the seal. A soft seat valve, in contrast, has an elastomer O-ring that sits on the metal body to create the seal. Each has its own advantages and disadvantages.
The Case for Hard Seat Valves
A hard seat valve represents the simplest, most versatile and cost-effective option. Without an elastomeric seal that that may limit applications as a result of concerns regarding chemical compatibility or extreme temperatures, the hard seat valve can be used in any application, as long as the metal is compatible with the medium.
Yet another advantage of the hard seat valve is a longer service life since the metal is more resistant to erosion and abrasion. Furthermore, depending on the flow characteristics of the application, the hard seat valve does not pose the threat of seal washout from a surge flow.
Although a hard seat valve can be used nearly anywhere for an endless number of applications, a primary downside is that it doesn’t form as tight of a seal when compared to a soft seat. Most hard seat check valves have an allowable leakage specification when closed. Although this specification is typically acceptable and still considered safe for most applications, there are times when any leakage is considered unacceptable. Applications involving fuel or gaseous media are prime examples where a leak of any kind could be catastrophic. The same can be said for any type of toxic chemical. All these applications would benefit from a soft seat valve to ensure there are no harmful leaks.
Considerations for Specifying a Soft Seat Valve
Soft seat valves, in contrast, offer better sealing and resistance to vibration. However, due to concerns of seal washout, they shouldn’t be used in applications with high potential for surge flows. The seals also present other constraints — temperature, for example, since the seals could fail prematurely due to extreme hot or cold temperatures. So, if you’re working with very high or very low temperatures, a soft seat valve may not be up to the challenge. Extreme cold could turn the elastomer to glass, at which point it could shatter. Typically, soft seat valves can perform down to temperatures of -60֯ degrees Fahrenheit or as high as 600 degrees Fahrenheit.
Soft seat valves offer better sealing and resistance to vibration but are limited in application due to concerns involving chemical compatibility with the elastomer seal.Parker Hannifin
Additional Considerations
Even among hard seat valves, there are differences. First, different materials can be used, depending on the application. Common metals include steel, stainless steel or brass. Stainless steel valves present the fewest compatibility concerns, but they are also the most expensive. The challenge is to balance the level of performance needed against the upfront cost.
The second difference is the size of the check valve. That is determined largely by the flow rate. Specifying the right size for the application is important for optimal performance, longer service life and cost efficiency.
How and where check valves are used is changing as a result of evolving market trends. Previously, they were primarily used for hydraulic applications. As a result of electrification trends causing systems to run hotter today, these valves are now also being used more often in cooling applications. The higher temperatures of the systems today mean that stainless steel, instead of steel, often must be used for the metal valve body.
Conclusion
The reality is that check valves are relatively small, less-visible components when compared to other parts within an operating system. As such, they are not always given the attention or consideration they deserve. Many companies may continue to use soft seat valves, for example, simply because they were used in the past. However, concerns regarding frequent replacement of worn-out O-rings or seals that are washing out should be flags that this might not be the best valve option for that particular application.
Contrarily, if leakage is wearing out system components prematurely, it could be a sign that a leak-proof option (soft seat valve) should be considered. If an insufficient amount of media is getting to some areas, this could be another sign that a different type of sealing option should be specified.
The bottom line is that there is a good reason why there are so many different types of check valves on the market. So make sure you’ve done your homework and documented ongoing problems so you can specify what size and material of hard or soft seat check valve works best for your application.