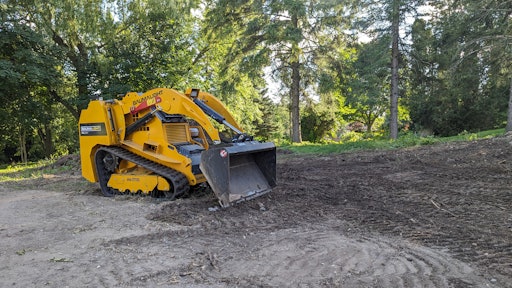
The integration of remote-control capabilities into off-highway equipment has historically been the domain of large manufacturers with substantial engineering resources. This technological divide has left smaller original equipment manufacturers (OEMs) struggling to meet growing market demands for sophisticated control solutions. This is especially true for off-highway OEMs, who often lack the resources to make headway in an expensive market.
A collaboration with compact equipment manufacturer, Baumalight, demonstrates how this barrier can be overcome through systematic engineering approaches and standardized integration protocols.
Figure 1: The transition to electronic control yielded benefits beyond remote operation, and operators reported enhanced responsiveness and precise control compared to the previous manual hydraulic system.Cattron
Transitioning to a digital, remote-controlled architecture
The catalyst for this engineering initiative emerged when Baumalight sought to expand beyond their existing implementation of Cattron engine control systems to address customer requests to remotely operate their mini skid-steer equipment. The technical challenge centered on integrating remote capabilities into their TRL740 series.
The complexity of this integration demanded a systematic, two-phase approach to system implementation. Phase one, spanning approximately eight months, focused on the controller implementation. This engine management controller enables precise control of mechanical and electronic engines through an advanced architecture featuring CANbus and Modbus communication protocols. The controller’s robust design, incorporating 22 configurable inputs and 10 high-side switch outputs, provides the flexibility required for complex machine control while maintaining reliability in demanding operational environments.
The transition from manual control systems to a digital architecture represented more than a simple upgrade. It established a framework for comprehensive machine monitoring, encompassing critical parameters across hydraulic systems and enabling predictive maintenance capabilities. The second phase of implementation, requiring an additional eight months, integrated the radio remote control system, completing the transformation to fully remote operation capability.
Developing a multi-system engineering approach
The technical integration of remote control capabilities centers on a multi-system design. The engine controller served as the primary control node, managing not only engine protection and performance optimization, but also providing an advanced interface for system configuration. This controller incorporated a high visibility display system engineered specifically for outdoor environments, enabling real-time monitoring of critical operational parameters through an extensively customizable interface.
The wireless control implementation leveraged a bellybox which incorporated a CAN-Based Machine Control Unit (CBMCU) receiver architecture. This system enables precise control through dual multi-axis joysticks, providing operators with up to six distinct motion controls. Critical to the system’s reliability is its redundant hardware and software, engineered to maintain operational integrity in demanding conditions with an IP65-rated enclosure.
The system’s unified control interface and docking mechanism enable seamless transition between mounted and remote operation. In this case, this extended beyond mechanical interfaces to include complete visual integration through private labeling capabilities, ensuring the control system presented as an integral component of the customer’s brand and by extension, its equipment design and packaging.
The technical scope of this implementation demanded extensive modifications to mechanical, electrical and hydraulic systems, while our custom-engineered wiring harnesses accommodated Yanmar and Kubota power plants. This dual-compatibility approach provides crucial flexibility in engine selection while maintaining consistent control system performance.
Figure 2: A large Pennsylvania-based waste management facility ordered the machine immediately after viewing demonstration videos, particularly valuing the remote control capability for handling hazardous materials.Cattron
Hydraulic integration challenges
Perhaps the most significant engineering challenge involved transitioning from manual hydraulic controls to electric-over-hydraulic systems while maintaining precise control characteristics. The solution required extensive development of custom control algorithms to ensure smooth operation under various load conditions.
Proportional control valve integration demanded particular attention to timing and response characteristics. We developed adaptive control algorithms that automatically compensated for temperature-induced viscosity changes and varying load conditions. The system continuously monitors pressure and temperature parameters, adjusting control responses to maintain optimal performance.
Safety system implementation
The safety dimensions extend beyond basic emergency stop functionality to include comprehensive system monitoring and fault detection. Independent processors continuously verify system state and operator commands, while algorithms monitor the machine and operational parameters.
The docking system, which allows seamless transition between local and remote operation, required particular attention to safety protocols. Redundant position sensing and automatic mode switching were implemented, ensuring operators cannot inadvertently activate remote functions during on-vehicle operation.
Figure 3: The remote control capability offers users an alternative to mounted operation and allows them to have better visibility and to maintain a safe distance when or working in dangerous environments.Cattron
Performance optimization
Initial testing revealed opportunities for performance enhancement through advanced control systems. Adaptive tuning capabilities that optimized system response based on operating conditions and operator input patterns were implemented. The system logs comprehensive performance data, enabling predictive maintenance to enhance operational lifespan.
Real-time monitoring extends beyond basic parameters to include diagnostic capabilities. The system tracks hydraulic system performance, engine operating characteristics and control system responses, providing operators and maintenance personnel with detailed insight into machine performance.
Future development paths
The applications for advanced remote control integration extend far beyond skid-steers. Engineering analysis revealed significant potential across multiple equipment categories, each presenting unique control challenges. Stump grinders, for instance, require precise manipulation in confined spaces, while conveying equipment demands variable speed control with extended operational range. Integrating remote capabilities into winch operations enables optimal positioning for complex pulling scenarios, enhancing safety and operational efficiency.
The safety features implemented in these systems represents a significant advancement in operational risk management. Consider heavy equipment operation implications: Beyond standard emergency shutdown capabilities, the systems incorporate monitoring and intervention protocols. A recent incident involving a wheel loader operator experiencing a medical emergency highlighted the critical need for supervisory override capabilities. The multi-layered safety architecture enables immediate machine shutdown through redundant control circuits, while maintaining system integrity.
Remote operation, however, represents just one aspect of a holistic control strategy. Integrating radio control systems with engine management and real-time telemetry, creates a more comprehensive solution that provides operators with control precision and performance monitoring.
The system’s modular design facilitates adaptation across various equipment categories, from compact concrete pumps to tracked generators and beyond, each benefiting from the underlying technical framework while maintaining application-specific control parameters.
Figure 4: Baumalight compact utility loaders come standard with an interchangeable, universal mini skid-steer “Quickattach” plate, the same plate that is used by all the major brands in North America.Cattron
Benefits for off-highway industry
The successful implementation of this control system architecture demonstrates the feasibility of plug-and-play remote control solutions for smaller equipment manufacturers. By providing standardized yet customizable integration tools, we’ve effectively lowered the barrier of entry for advanced control systems for smaller OEMs.
This development has broader implications for the off-highway equipment industry. Increased competition in the remote-controlled equipment segment will drive innovation and improve accessibility to broader and more advanced features. Standardized safety protocols establishes benchmarks for equipment operation, while modular systems will enable smaller manufacturers to implement sophisticated controls without extensive development resources.
Improving accessibility
The integration of remote control capabilities into compact equipment represents more than technological advancement; it demonstrates how an entire industry can move toward greater feature accessibility. As market demand for remote operation capabilities continues to grow, this approach provides smaller manufacturers a path to compete effectively in an increasingly automated market.
The successful implementation shows how complex control systems can be successfully deployed by smaller OEMs when proper integration protocols and support structures exist. This model of accessible integration, combining advanced control capabilities with straightforward implementation, establishes a framework for future development in the off-highway equipment sector.